Pure niobium crucible
A niobium strip is formed into crucibles for the manufacture of
synthetic diamonds in a wide range of applications. In some cases, block
synthetic diamonds are required, which are obtained by placing the
carbon material in a niobium crucible and exposing it to high pressure
and high temperature .
Niobium crucibles are made of sheet material by deep drawing. The
quality and surface quality of these crucibles are critical to the final
quality of synthetic diamonds. To meet the demands of deep drawing and
quality requirements for synthetic diamonds, Raytec metal engineers have
made significant improvements to our niobium sheet, which solves the
problems and problems associated with making crucibles.
Niobium Crucible Defect Prevention
There are many variables to consider when designing a deep drawing
process. Incorrect configuration at any stage can lead to defects in the
final deeply drawn component.
o Crumple in the flange due to low holding force.
o Wall wrinkles occur when the wrinkled flange is pulled into the cup or
the gaps are very large.
o Tearing occurs due to high tensile stresses that cause thinning of the
sheet. The gap also occurs due to sharp angular radii, high length to
diameter ratios (L / D), high pressure gasket loads and high stamp
loads.
o An earring occurs when a material is anisotropic (ie, directivity in
properties)
o Surface scratches occur if the punch and die are not smooth or if
process grease is insufficient.
o Radial cracks on the flanges and the edge of the bowl due to
insufficient ductility of the metal.
o Orange peel (surface roughness) is found in coarse-grained metals.
The most common material defect problem is the orange peel due to the
coarse grain size. A related microstructure of niobium may show poor
flatness and smoothness of a deeply elongated cup, since each grain
tends to deform independently and unevenly. Poor flatness and / or
smoothness can lead to the formation of synthetic diamond, which
requires excessive grinding. The coarse-grained structure can also cause
sheet tearing during deep drawing operations.
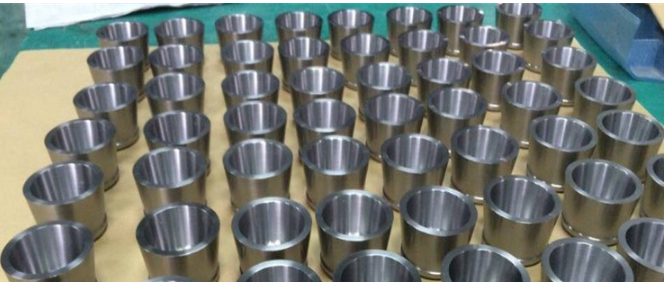
Niobium
Cobalt
Iron
Carbon
Sulfur
Copper
Zinc
Lead
Total Impurities
99.99
<0.00002
0.002
<0.01
0.0002
0.00005
0.00005
0.00002
<0.01
Diam
thickness
length
width
purity
Details

Foil
0.03mm -0.8mm
>3000mm
2mm-150mm
99.99%
Details

sheet
0.03mm-50mm
100mm
100mm
99.99%
Details

wire
0.025mm
-0.05mm
7000-8000m
99.99%
Details

Stab
2.0mm
-150mm
<1000mm
99.99%
Details

powder
50nm- 20μm
99.99%
Details

Pellets
6mm-13mm
99.99%
Details

granules
6mm-13mm
99.99%
Details

Sputter
target
3mm-300mm
O30--2000mm
99.99%
Details

crucible
30ml-50ml
99.9%
Details

mesh
0.05-2mm
hole:0.3X0.6mm, 0.5X1mm
............20X40mm
99.9%
Details

foam
0.3-10mm
100mm
100mm
Details
A niobium strip is formed into crucibles for the manufacture of
synthetic diamonds in a wide range of applications. In some cases, block
synthetic diamonds are required, which are obtained by placing the
carbon material in a niobium crucible and exposing it to high pressure
and high temperature .
Niobium crucibles are made of sheet material by deep drawing. The
quality and surface quality of these crucibles are critical to the final
quality of synthetic diamonds. To meet the demands of deep drawing and
quality requirements for synthetic diamonds, Raytec metal engineers have
made significant improvements to our niobium sheet, which solves the
problems and problems associated with making crucibles.
Niobium Crucible Defect Prevention
There are many variables to consider when designing a deep drawing
process. Incorrect configuration at any stage can lead to defects in the
final deeply drawn component.
o Crumple in the flange due to low holding force.
o Wall wrinkles occur when the wrinkled flange is pulled into the cup or
the gaps are very large.
o Tearing occurs due to high tensile stresses that cause thinning of the
sheet. The gap also occurs due to sharp angular radii, high length to
diameter ratios (L / D), high pressure gasket loads and high stamp
loads.
o An earring occurs when a material is anisotropic (ie, directivity in
properties)
o Surface scratches occur if the punch and die are not smooth or if
process grease is insufficient.
o Radial cracks on the flanges and the edge of the bowl due to
insufficient ductility of the metal.
o Orange peel (surface roughness) is found in coarse-grained metals.
The most common material defect problem is the orange peel due to the
coarse grain size. A related microstructure of niobium may show poor
flatness and smoothness of a deeply elongated cup, since each grain
tends to deform independently and unevenly. Poor flatness and / or
smoothness can lead to the formation of synthetic diamond, which
requires excessive grinding. The coarse-grained structure can also cause
sheet tearing during deep drawing operations.
Niobium | Cobalt | Iron | Carbon | Sulfur | Copper | Zinc | Lead | Total Impurities | ||
---|---|---|---|---|---|---|---|---|---|---|
99.99 | <0.00002 | 0.002 | <0.01 | 0.0002 | 0.00005 | 0.00005 | 0.00002 | <0.01 |
Diam | thickness | length | width | purity | Details | ||
---|---|---|---|---|---|---|---|
![]() |
Foil | 0.03mm -0.8mm | >3000mm | 2mm-150mm | 99.99% | Details | |
![]() |
sheet | 0.03mm-50mm | 100mm | 100mm | 99.99% | Details | |
![]() |
wire | 0.025mm -0.05mm |
7000-8000m | 99.99% | Details | ||
![]() |
Stab | 2.0mm -150mm |
<1000mm | 99.99% | Details | ||
![]() |
powder | 50nm- 20μm | 99.99% | Details | |||
![]() |
Pellets | 6mm-13mm | 99.99% | Details | |||
![]() |
granules | 6mm-13mm | 99.99% | Details | |||
![]() |
Sputter target |
3mm-300mm | O30--2000mm | 99.99% | Details | ||
![]() |
crucible | 30ml-50ml | 99.9% | Details | |||
![]() |
mesh | 0.05-2mm | hole:0.3X0.6mm, 0.5X1mm ............20X40mm |
99.9% | Details | ||
![]() |
foam | 0.3-10mm | 100mm | 100mm | Details | ||